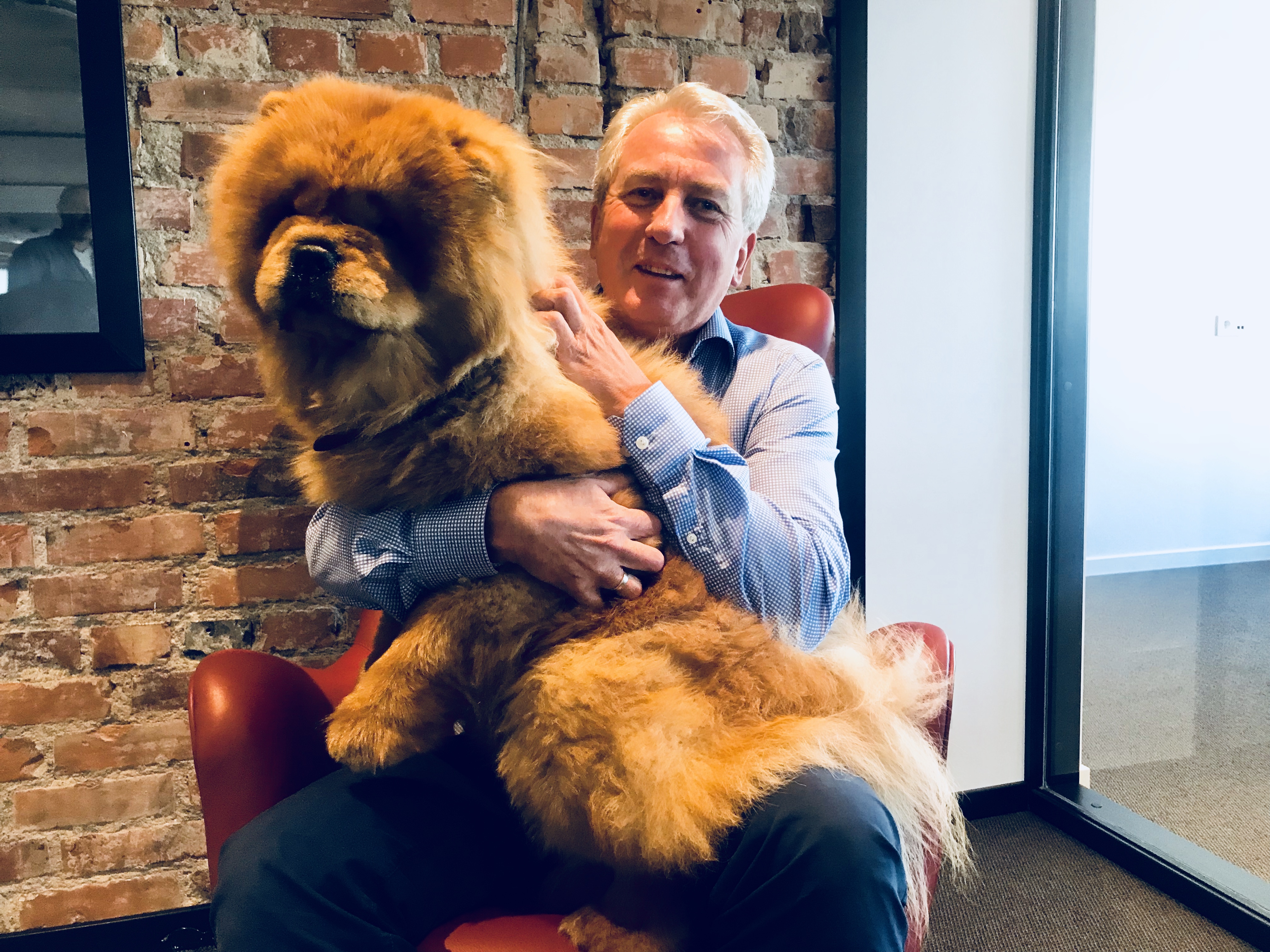
A furry dog on the lap is sort of Thermal Management when you are cold! Senior Technical Advisor at Elmatica, Josse Johnsen, tells you how to manage on Printed Circuits as well.
Printed Circuit Boards (PCB) are the fundamental part of all electronic devices, making the electronic components connect and also work as Thermal Management. With this in mind, it’s a good idea when designing a PCB, to always have Thermal Management in mind. How many layers, how thick are they, what materials are used, copper content, vias, and placement of them?.
When dealing with Thermal Management, all pieces of the PCB puzzle plays an important role.
In this edition of Josses Corner, I will discuss different solutions to obtain Thermal Management when designing PCB.
The PCB material, insulation between layers, is a poor heat conduct. The ability of the copper to transport heat is far better.
Typical for an FR4 material the thermal conductivity λ~ 0.22 W/mK, and for copper it is λ~ 390 W/mK
A full-size heatsink can be external or internal.
– Internal it is Metal-Core layers or Thick-Copper layers.
– External it can be pre-bonded (IMS) or post-bonded.
Local Heat-Dissipation
Most common is the use of Thermal Vias. They can be mechanically drilled blind or through vias.
Laser, stacked mVias, become more common, especially with low i/o pitch components.
An alternative that will give better heat dissipation is the use of a local Cu-Coin.
This can be a Bonded Cu-Coin, Press-Fit Cu-Coin or Embedded Cu-Coin.
Options:
-Heavy copper planes, cu thickness up to 210µm (6 oz) with UL Approval)
-Thermal via plated or filled with a conductive paste
-Metal plate spreader
-Coin attached – by tape or soldering
-Embedded Coin
Dielectric used:
-RF & high-frequency material. Typical of Roger, Arlon, Taconic, Isola….
Heat Sink PCB Design Options:
-Heavy copper / or Vias plated with Cu
-Metal back bonded to RF material. Typical single sided boards
-Coin attached by conductive adhesive into cavity PCB.
-Coin embedded inside the PCB.
Thick copper inner layers. Thermal vias filled with conductive paste.
Metal back bonded to RF material, single side cu.
Option 1: Heavy Copper PCB
-Boards design to carry high current
-Heat generated is distributed throughout heavy copper traces up to 210µm with UL approval.
-Boards to be designed with compatible material
-Higher heat dissipation traditionally needs external devices as well. As chassis or external heat sink.
Option 2: Metal Backed PCB
Application: Power Amplifier Module (RF board)
Key Attributes:
– Copper Based Metal Plate PCB:
Copper heatsink and RF-60 PTFE material. This is a ceramic filled fiberglass substrate.
Other materials can also be used.
-Controlled Depth Cavity where plated holes connect to the metal plate.
-Thick Copper Plate. Challenges:
-Mechanical Routing & Drilling. Need to handle both hard Cu & soft PTFE
Option 3: Coin Attachment
Coin Assembly onto Cavity PCB for Heat Dissipation:
-Most common with a Conductive Adhesive Layer
-More seldom with Solder Reflow Attachment. This need to be clarified with EMS, Assembly house.
– Also, a thick copper plate can be pretreated and contain towers that act as coins.
Backplate with 5 coins, fabricated in one piece.
The plate measures 42x42mm. Reminding plate thickness
0.5mm and hight of coins 1.1mm. Total 1.6mm.
Some figures:
One via hole 0.5mm plated with 25 µm copper = λ~ 0.6W/mK.
One via hole 0.5mm plated with 30 µm copper = λ~ 0.7W/mK.
One via hole 0.5mm plated with 25 µm copper
and filled with conductive silver paste = λ~ 0.63W/mK.
The effect of using conductive paste is limited and normally not used.
The coin technology you can see here is available from some of our approved
PCB manufacturers in our portfolio. If you have questions or would like to discuss any project you are struggling with, planning or looking into?
Feel free to reach out to me!
Josse
Previous blog posts from Josses Corner: